No list of hurdles I encountered with the Rig would be complete without addressing the engine itself. When the dealership changed the oil in the truck they found a significant amount of metal flakes on the oil drain plug (which is magnetic, just for this purpose). There was enough accumulation that they were prompted to dissect the old oil filter, which revealed a concerning amount of metal being captured. They informed me that said metal was likely coming from either one or more of the crankshaft journal bearings or one or more of the piston rings and there was enough of it that, it was a matter of when, not if, it would experience a catastrophic failure. Essentially, if any of those bearings or rings fail, the resulting mechanical chaos would result in the swift destruction of the engine or what they colorfully described as a “grenade”. I wasn’t totally unprepared for this news, but I had thought it would come a year or two down the road.
I spoke to the service manager at length about the issue and he was extremely helpful in answering my many naive questions. I was concerned that driving the 1600 miles from Florida to Michigan could have caused the issue or letting it sit for nearly two years without starting. He said while driving it would have added to the wear, neither had anything to do with causing the issue and it had likely been shedding metal for some time before it was retired. From what I read on the subject, it was more likely to be a journal bearing failing rather than a piston ring, as the latter would have likely lead to blow-by in the early stages of failure, which we weren’t seeing in my engine. Blow-by occurs when combustion gases leak around the piston and escape into the oil galleries of the engine. This results in excessive soot and diesel fuel in the oil, which can be extremely corrosive. While I didn’t have my oil tested I did do a fairly simple test for the presence of diesel fuel in the oil (and coolant) and did not see evidence of either.
It’s fairly common to have the oil tested at every oil change in heavy duty diesel engines. This chemical analysis can detect microscopic amounts of metals and other substances, such as diesel fuel an coolant, giving you early notice of a potential developing problems. The company that does the testing will also compare it to any prior analysis, as well as to other similar engines. Of course, once you have metal flakes big enough to see with the naked eye, you’re way past the point of any kind of useful intervention.
This all came about sooner rather than later as I had made some flawed assumptions back when I was searching for a truck to buy and evaluating this specific vehicle. While my engine had a seemingly low 86,000 miles on it, given it’s age, it also had 8,700 hours (the engine management computers in medium and heavy duty trucks keep track of engine run hours as they can spend a lot of time idling or running other equipment via a PTO (Power Take Off), thus accumulating wear, but not miles on the odometer.) I knew the hours were high given the comparatively low mileage, but based on my limited research and general ignorance on the subject, I initially (and incorrectly) calculated that every hour of engine run time was equivalent to 20 miles of wear and tear. In reality, as I learned through more thorough research, a more accurate number would have been 40 miles of equivalent wear and tear, especially given that my truck was likely rushing to and from emergencies with above average periods of idling while on scene. The ambulance computer would also automatically increase the RPM of the engine to build air faster or, presumably, increase the output of the AC compressors as needed in the hot Florida sun. Of course, some of those engine hours were spent actually accumulating miles, so it’s not as clear cut as just multiplying by the entire 8700 hours. For simplicity, I decided half the hours would be attributable to idling and the other half to actual drive time. Using my flawed 20 mile estimate, I had calculated that 4,350 (half of 8700) hours was equivalent to 87,000 miles of wear, which when added to the actual mileage of 86,000 miles comes out to 173,000 effective miles of wear and tear, which seemed reasonable for an eleven year old truck. If I had instead used the more accurate 40 miles per engine hour, I would have come up with 260,000 miles of wear and tear, which may or may not have raised alarm bells in my mind. Additionally, keep in mind that when I say engine, I’m including all the accessories that bolt to the engine block, including the fuel pump, oil pump, oil cooler, oil separator, high and low pressure turbos, air compressor, EGR cooler and EGR valve. In short, my engine and all the important bits bolted to it was worn out and the metal flakes in the oil were indicative of imminent failure.
This presented a number of options on how to proceed, none of which were particularly appealing and some of which were gob-smackingly expensive (obviously I chose that one. In for a penny, in for tens of thousands of dollars). The following were my options to consider:
Option 1: Do Nothing (0)
The engine did run fine as it was, despite the fact that it was apparently in the early stages of tearing itself apart inside. It had made it the 1600 miles from Florida and was still running. The downside was that they couldn’t tell me if it was going to fail in 100 miles, 1000 miles or 5,000. This meant when it came, the failure would almost certainly occur at an inconvenient time and place, leaving me stranded.
I also had to consider a future sale of the truck. With a terminal engine problem it was essentially un-salable for anything other than salvage. The two plus years of work I put into the conversion and the not inconsiderable sum invested thus far would all be for naught. If I walked away from it, I could strip a lot of the electrical equipment and to sell piecemeal on eBay, but I would only recover a fraction of the cost of all that stuff and have to deal with the hassle of removing, storing, listing and shipping it. More importantly, I still wanted to try the live aboard thing so I wasn’t keen to just give up. You might point out that I could have tried the live board / van life by simply renting a van for a few months. However, as I’ve mentioned in numerous posts, more than half the reason for doing this project was doing the conversion work myself and learning all the technical skills that went along with that. I’m not a turn-key kind of guy.
Option 2: In-Frame Rebuild ($$)
Other than doing nothing, this was the least expensive option. Essentially, it involved replacing the high-wear items inside engine; the pistons, piston arms, piston rings, piston liners, crankshaft bearings and head gasket along with the head bolts. This is a common enough repair that all the necessary parts are sold as a rebuild kit for your particular engine. Besides the parts kit, it would also involve approximately 20 hours of labor. While an in-frame rebuild would correct whatever issue was the source of metal in the oil, they might also find additional damage to other parts once they got into the engine, at which point I might have to make the leap to Option 3 or 5 anyway and about half of the labor cost involved would go to waste.
I also had to consider that while this would replace the aforementioned high-wear items in the core engine, it would not replace any of the external accessories bolted to the engine, the majority of which were the same age as the engine; fuel injectors, valves, intake and exhaust manifolds, high and low pressure turbos, oil cooler, EGR cooler, oil pump, fuel pump, air compressor, EGR valve and oil separator along with all the mounting gaskets would not be replaced and would also certainly continue to cause problems. As I had already opted to replace the air compressor and EGR valve, those would be new, but all the other components could fail at any time and lead to expensive diagnostics and repairs as well as more time where I wouldn’t be living in my truck and would have to make other arrangements.
Option 3: Used Engine ($$$)
This option involved sourcing an identical engine from a wrecked or scrapped truck and swapping it with mine. While this engine would presumably be in good working order, I would have no way of knowing how it was treated or what hidden issues it might have. Given the age of my truck I was also advised that it might take several months to find a suitable used engine. As with the In-Frame Rebuild, all the accessories that attached to the engine would simply be brought over from my engine and thus those would all remain a potential source of more problems.
Option 4: Long Block Rebuild ($$$$)
This is similar to the in-frame rebuild, but more with a lot more labor. With a long block rebuild, the engine is completely removed from the chassis affording easier access to all parts of it. Like the in-frame, the high wear items would be replaced: pistons, piston arms, rings, crankshaft bearings and head gasket. In addition, most of the gaskets around the engine would also be replaced. The parts cost is only slightly more, but it adds another 20 hours of labor for 40 total, which at $185 per hour, is not a trivial amount. However, just like the two previous options, all the accessory components would still be brought over from my engine, thus those potential time bombs would keep right on ticking.
Option 5: Trimmed Engine ($$$$$)
A Trimmed Engine is a factory refurbished, 95% new engine with all the accessories already bolted on. They re-use a few minor items from the old engine, but nearly everything is new (or refurbished). This option is only a couple thousand more than Option 3, but includes all new everything: Intake and exhaust headers, fuel injectors, valves, both turbos, oil cooler, EGR cooler, oil separator, fuel pump, high pressure oil pump and air compressor. All the internal bearings and gears would be new as well: all the timing gears under the front cover, crankshaft and the critical front and rear thrust bearings. Basically everything involved in burning diesel fuel and converting into torque which the transmission then turns into forward motion.
Besides the rather staggering cost, which would buy a decent new car, the only real downside to this option was that the air compressor and EGR valve I had already replaced, at no small expense, were included with the trimmed engine, so essentially, all the labor and parts I already paid for would go to waste. Even though these parts were essentially new they would have to be returned as part of the core of my old engine.
During the engine removal they also found that the engine and cab mounting bushings were worn out. Given those are easier to replace with the engine already out of the chassis, I went ahead and approved those repairs as well, along with a cooling fan bearing, which was showing signs of advanced wear.
The Decision
Given the cost of the various options I took a week to think things through and after careful consideration, I decided to proceed with the trimmed engine. To begin with, the only viable options in my mind were Option 2 or 5. With Option 2, the in-frame rebuild, I would get away with a comparatively inexpensive repair bill, but I would face problems with all the other components, nearly all of which were the same age as the core engine. Replacing all those accessories individually, as they failed, would ultimately cost me more than the trimmed engine and would mean additional downtime while the truck was in the shop, not to mention possible breakdowns in inconvenient places, expensive heavy tows, the additional cost of diagnosing each issue as it arose and the stress that comes with dealing with all that crap. This way, it’s all done now while I have an alternative place to stay, before I hit the road long-term, and by a reputable dealer.
Another thing I had to consider was the time it would take to do any of the repair options. In-frame and long-block rebuilds and engine replacements are complicated procedures. At the dealer where I had my truck they had a 4-6 week waiting list. Once I made the decision to move forward and gave them a deposit they were actually able to start on my truck earlier than expected since it was just sitting there in their lot. While they were waiting on parts for the truck getting a rebuild before mine, they were able to bring mine into a spare bay and make some progress. As eager as I was to finish the conversion work and get on the road, I was also content to give it a few more weeks and make sure the job was done right. Ultimately it ended up taking them about three and half weeks to complete the replacement and finish all the testing. It was frustrating to have things drag on this long, but I let things run their course.
Once the new engine is installed and everything reattached, they fill it with vital fluids and then do an extensive break in road test to make sure everything is optimally tuned and running perfectly. I’m told I wont need to do any kind of a break in period myself, although they said it wouldn’t hurt if I changed the oil after 4000 miles rather than the recommended 15,000 (which seems absurdly high to me anyway).
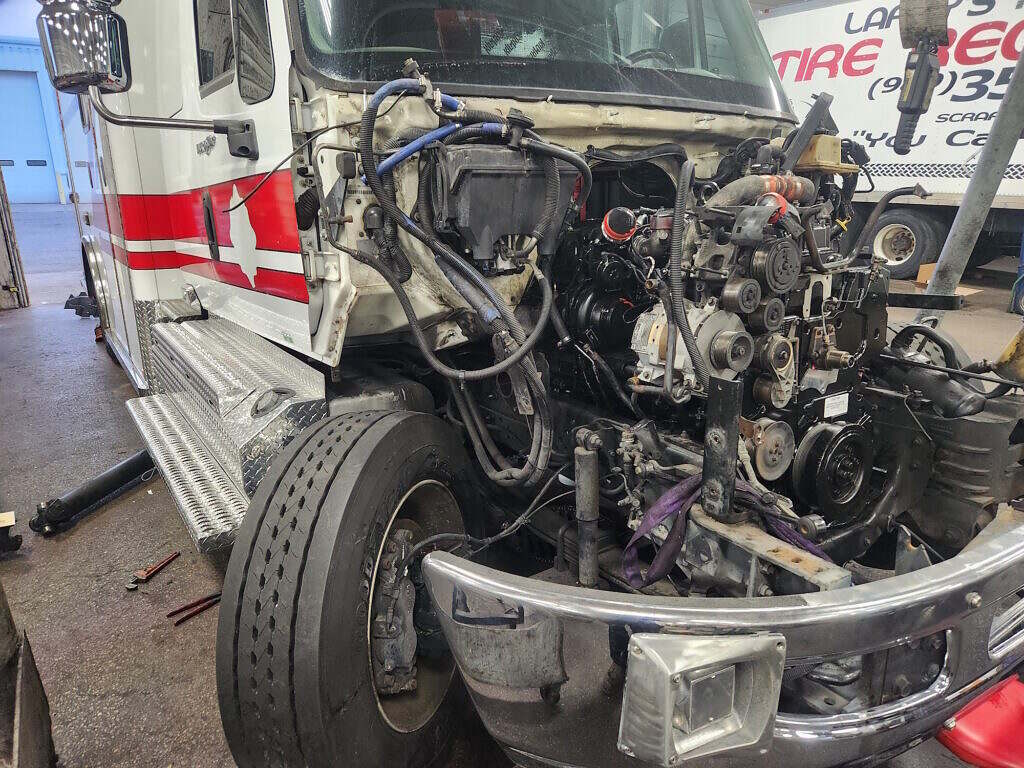
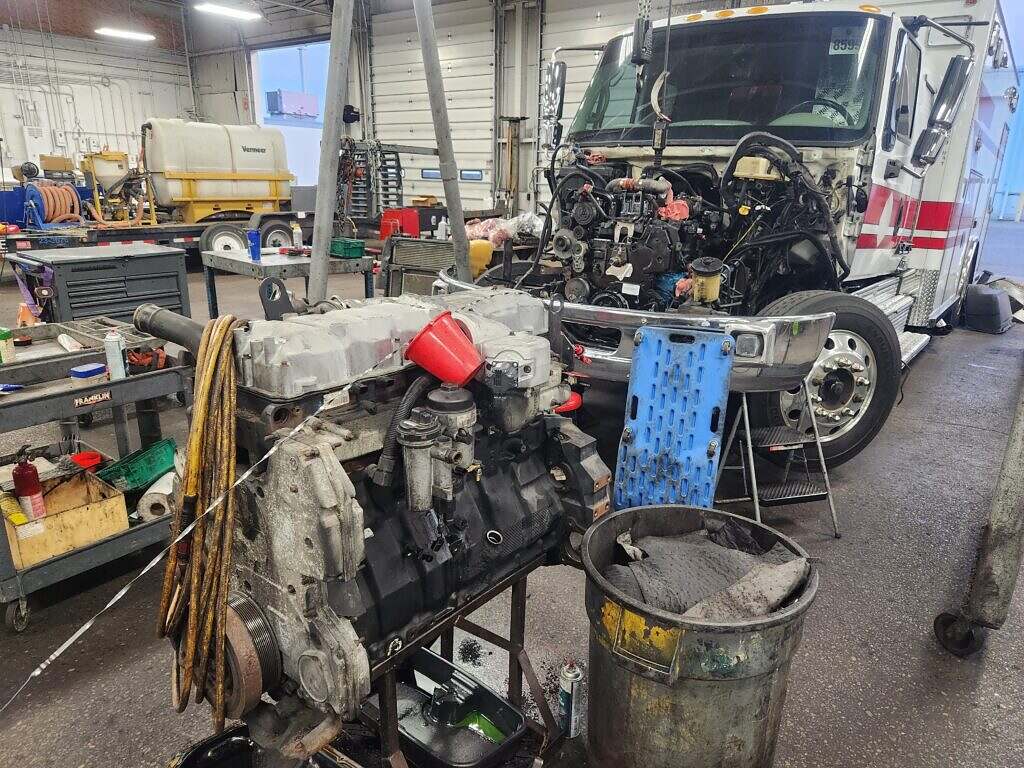
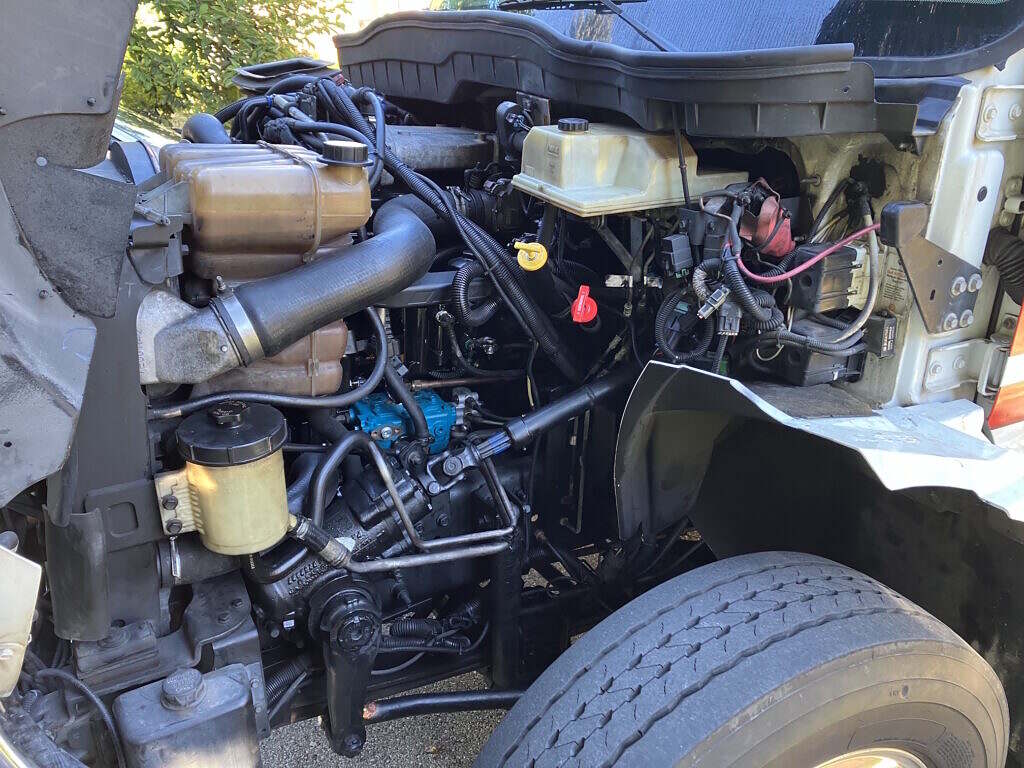
The final result with the new engine installed doesn’t look like much because it’s mostly covered up by the many air and coolant hoses and other brick-a-brack. From the driver’s side you can just make out the gleaming black engine block buried under everything and the blue air compressor. On the plus side, the new engine it is very noticeable from the driver’s seat, in that it runs like a champ and doesn’t generate a single warning lamp or dash alarm.