Herein I document the notable injuries I’ve sustained as well as my adult beverage of choice for this project. As I write that sentence, it occurs to me some might assume a direct correlation between the two. Or, as I suspect, an inverse correlation; that is, the more beer I drink the fewer injuries I sustain. Hmmm, something to ponder over a few beers I should think.
While I’m not overly safety conscious, and frequently, knowingly, do downright dumb shit, I do have a healthy respect for the ability of power tools to maim. While I wear hearing, eye, skin and breathing protection most of the time, I don’t ALWAYS do so. The one exception is when using the Milwaukee grinding wheel. I’ve watched one to many YouTube/TIkTok videos of grinding wheel accidents to not wear several layers of eye protection when using it. It very much feels like it’s just waiting for the chance to rip into a limb or spit fractured pieces of a cutoff wheel into one’s face. I call it “The Mangler”. I’m often tempted to just pick it up and cut something quick, but I force myself to slow down, put on adequate PPE and consider the job to be done to make sure what’s underneath/behind it or what nearby fuel source might be ignited by the sparks.
One lesson I learned the hard way (several times over) was that it’s generally not a good idea to wear knit gloves when using any kind of power tool that spins. This is because sharp, spinning things have a tendency to snag the knit cuff and pull your extremities into the maw of the beast, as it were. One particularly painful lesson was when I was using a wire wheel on a cordless drill to remove the glued on padding from the fiberglass ceiling panels in the cab. A brief moment of not paying attention and the wheel grabbed the cuff of my left glove, which then began to pull the wheel into and along my forearm. Even though I instantly let go of the trigger, it still managed to give me a good 6″ of painfully deep gouges up the inside of my forearm. Yes, I’ve had my tetanus booster.
It’s not like I need assistance from power tools to injure myself. One evening I was up the ladder working through one of the emergency light mounting holes to reach some electrical wiring. As is my way, I was leaned way to far over on the ladder in order to reach as far into the hole as I could. The ladder began to slide out from under me and I was left hanging by my bicep. Fortunately, I was directly over Locker B, which has short doors and I was able to get a foot on one of them to partially support my weight. Of course, those doors have hinges and so immediately began to also rotate out from under me. Had I lost my footing I have no idea how I would have escaped that position. The movie 127 Hours flashed through my mind more than once before I was able to coax the ladder back under me with the tip of one shoe. Left one helluva bruise.
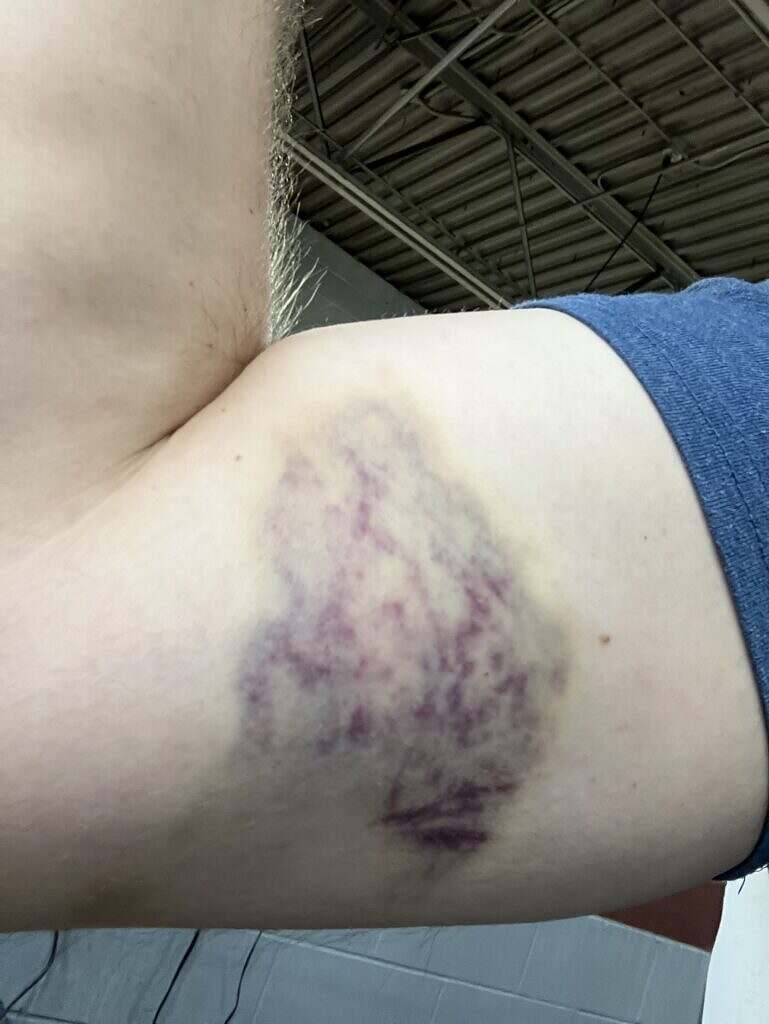
The most numerous injuries, by a long shot, are the near constant burns to my fingers and palms. For some reason, I can never quite remember the simple lesson that friction makes things hot and it is almost a daily occurrence for me to be grinding or polishing something only to then grab it and get re-taught that seemingly simple lesson. Polishing screws and bolts is particularly painful as the most effective way to polish them entails holding these small items by hand and spinning them between your fingers as a polishing head spins at 15,000 RPM approximately a centimeter away. It’s not so much any one screw/bolt/washer as it is the shear volume of these I’ve polished, which at last count was over 800. I polish these fasteners using a die grinder, which while fast, fortunately has very little torque, thus it’s ability to burn but not maim. Each fastener gets at least 3 steps; first with a course pad, then a fine pad and finally with a compressed wool pad and brown tripoli polishing compound so that’s something on the order of 2400 polishing passes at this point.
By far the most painful injury I sustained (so far, fingers crossed) was while I was teaching myself to weld. I was wearing shorts, which is obviously super smart in the presence of molten metal spattering all around. At one point I neglected to tuck my legs under the bench I was welding on and a molten glob of aluminum did a perfect swan dive into my shoe. Having become quite familiar with the instant pain of hot metal burns by this point, I anticipated a quick flash of pain and then relief. However, this was a rather large glob of aluminum and it continued to burn down into my flesh as I tried to kick it away; my hands being otherwise occupied, while I screamed a litany of profanities into my welding helmet. It left a small, but incredibly painful hole in the top of my foot, which took some 8 months to heal completely.
Despite owning an ambulance, I lack the typical kind of first aid supplies one might expect to keep on hand in a shop environment. My excuse is that I never think about it until I’m injured and bleeding. My go-to “bandaid” is toilet paper and painters tape.
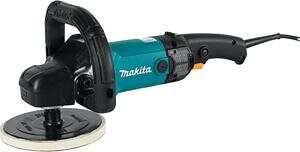
This post was written over a span of many months as I accumulated injuries. Upon rereading I took particular note of paragraph three and my caution about wearing knit gloves around spinning tools. My most serious injury was a direct result of not following my own advice (again.) The other scary-powerful tool that I use is a Makita polishing wheel. It’s as powerful as the grinder, but because it polishes instead of cuts or grinds, causing sparks to fly, I discounted the danger it posed. The Makita also has a helpful, yet insidious feature that allows one to lock the trigger in the on position. This makes sense when polishing, as after even a few minutes of wrestling the torque of this thing you start to get cramps if you also have to keep the trigger pulled. This is typically fine, since when you’re properly holding it, your finger hovers over the trigger and a quick flick is all it takes to release the trigger lock. As is probably predictable, I was misusing the polisher when it bit me. In order to polish small parts it’s necessary to grip them tightly with two hands. The polisher has so much torque that if you don’t hold tight it will rip the part out of your hands and fling across the shop. As I only have two hands I would often clamp the polisher upside down to my work bench. This would essentially turn it into a bench polisher, with none of the safety features or stability of a real one. The one flaw in this is that polishing generates heat and the smaller the part, the faster that heat accumulates. To avoid burning my fingers (again) I would often wear gloves. I was happily polishing along at the full speed of 3500 RPM in this manner when in the blink of an eye my glove was snagged by the metal in the center of the wheel and was pulled into the wheel along with my hand that was still inside it. I tried to jerk my hand away, but all I succeeded in doing was dislodging the polisher from the bench so it was hanging from my now crunched hand still trying to spin at it’s designated RPM. I managed to kick the cord loose from the extension cord to get the motor to stop. At this point the wheel had popped off the metal center and my glove and fingers were in a knot wrapped around the hub. Blood began splattering on the tool, down my leg and onto the floor as I managed to slowly back the wheel one handed and release my fingers. There was no pain despite the copious blood flow and my immediate thought was how dirty my hands were. I went over to the sink and flushed the wound with water and used some soap to wash my hands as best I could. I couldn’t really see the wound given the blood, dirt and water. I wrapped it in paper towels and gave it a couple wraps of painters tape. I also took a quick pic of the polishing wheel in case the doctors might need to see what inflicted the damage, drank the rest of my beer (no, it was not a contributing factor), locked up the garage and drove to the local ER a few miles away.
It’s a bit hard to say I was lucky, given this happened on my birthday, but in a way I was. I didn’t break any bones or cut any tendons, both of which would have resulted in long recoveries and significant delays in work on the truck. As it was, I ended up with 9 stitches, very little pain and a complement from the ER doc on my use of painters tape as a triage bandage. The cut itself never really hurt, even after the adrenaline and local anesthetic wore off, but my knuckles took quite a beating and there was a fair amount of swelling.
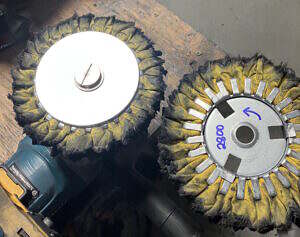
Adding insult to injury, they do sell so-called “safety flanges” for this type of polishing wheel. I had opted not to buy them, reasoning that if they were important they would be included with the polisher. I’ve since bought a set of said safety flanges and an extension for the bolt that holds the wheel on so it can stand off several inches and not create a pinch point. After the fact it also occurred to me that rather than hand-holding small parts I could instead screw them down to the work bench and hold the polisher in a normal manner.
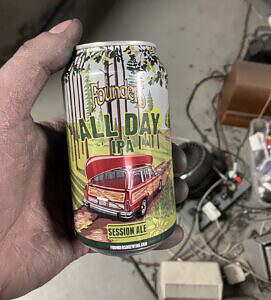
One of the most enjoyable aspects of this project has been the near daily consumption of Founders All Day IPA. Many an hour has been spent and many a problem has been solved standing back and considering some aspect of the project while imbibing a frosty can of this fine ale. As it happens, All Day is brewed a mere two miles from the garage. It is damn tasty stuff and the only beer I can think of that is better in a can than in a bottle.
Having purchased my fridge early on, I quickly realized the logic of plugging it in and using it to keep a ready supply of All Day on hand. I don’t drink to excess, but dang there is just something enjoyable about sipping a beer while working on a project like this. When the weather is nice, it’s quite pleasant to sit out back and enjoy a cold one or three and a good cigar while listening to the roar of the expressway on the other side of the building and contemplating my latest creative challenge or crushing disappointment related to the truck.