This post will detail the module flooring. I’ll tackle the cab floor in another post as it’s completely different from the module floor. As discussed in the ceiling post, a measurement I wanted to maintain was the overall height in the module. I put considerable effort into a ceiling solution that minimized the loss of height and therefore a similar amount of effort into the floor. The existing floor was a commercial grade dark blue vinyl sheet with a raised circular tread pattern. It was installed with a 3″ lip running up the walls, I assume to prevent bodily fluids from soaking into nooks and crannies and make it easy to hose out said bodily fluids at the end of a shift. I was originally just going to leave it, but given my ceiling was dark blue I felt a lighter floor would considerably change the feel of the interior and lighten it up a bit. Also, the existing floor had an eight foot long, two inch wide slot cut out of it that I didn’t really want to look at.
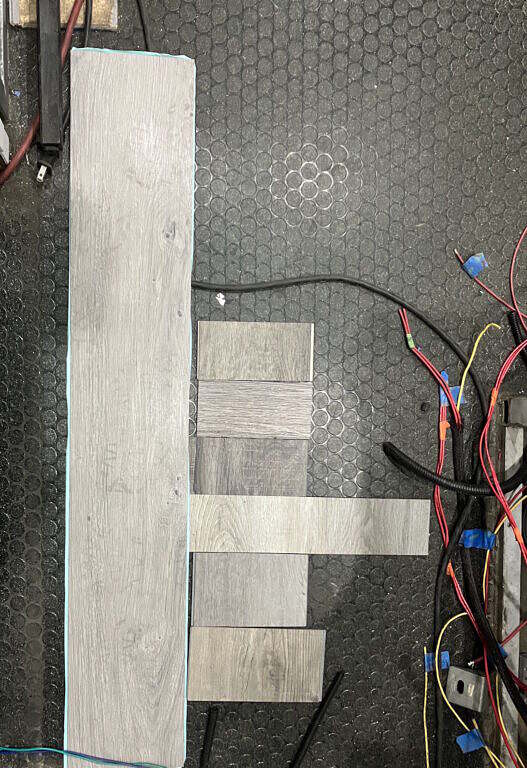
Originally I had planned to replace the vinyl floor with a basic wood-patterned vinyl sheet. I had considered manufactured plank flooring, like Pergo, but found it much to thick. During my research I stumbled across vinyl plank flooring that splits the difference between basic vinyl floor and Pergo. It runs 4-10mm thick and typically has interlocking edges and some type of noise deadening backing. Wandering around Home Depot one day, a display in the flooring section caught my eye with the name “Sanibel Oak”. Sanibel, for those who don’t know, is an island on the Gulf side of Florida, near Fort Myers, where my parents had wintered. The Sanibel Oak was a bit dark for me, but examining the display further I found another color/style called “Useppa Oak”, which was exactly the shade I was looking for. Useppa is also an island, though private, in the Pine Island Sound on the gulf side of Florida where some close family friends had a house for many years where I had spent some time. It’s pure marketing b.s. to label this stuff after islands in Florida as I’m fairly certain they haven’t been logged in a hundred or more years, but it was kind of a fun coincidence nonetheless.
In my never-ending quest to keep things simple and maintainable when designing, I didn’t want to use any adhesive or fasteners on the floor. Once I knew the vinyl plank I was using was 5mm thick, I was able to trim the existing vinyl edging such that it created a lip the vinyl planking would slip under while still being removable.
The plank flooring is made with a semi random wood grain that repeats every couple of boards so you’re supposed to mix four or more boxes to avoid repeating patterns. Because I only bought three boxes of the stuff, I didn’t have a whole lot of variability and had to put some effort into laying out the planks so the repeating grain wouldn’t be obvious. I also had to deal with the fact that because I wanted a row of full-width planks on the passenger side and given the way the edges are designed to interlock, I had to install it from the front-right of the module to the back-left, rather than the other way around.
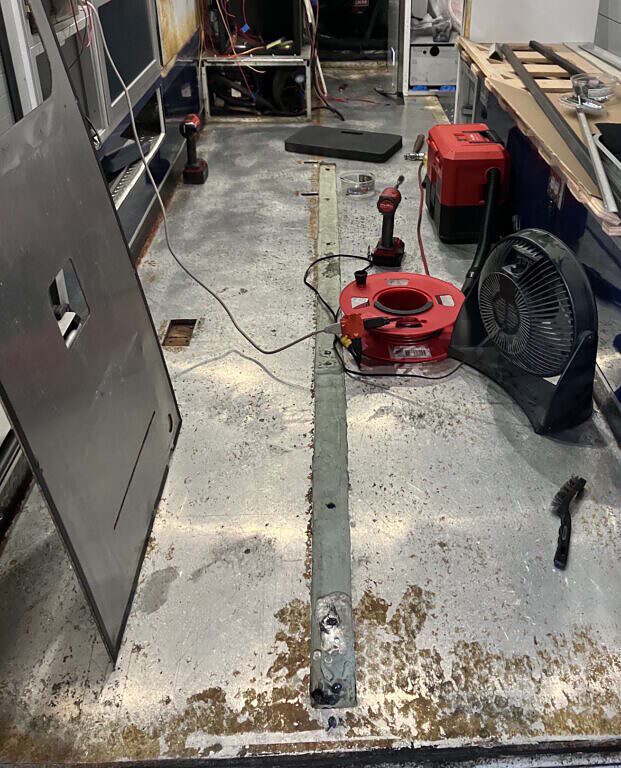
Before I got started with the installation I first had to do something with the stretcher track that ran 2/3 of the length of the module. This track had rough and irregular surfaces and edges so I needed something that could fill in all the nooks and still allow it to be finished flat so there would be no lumps in the plank flooring. Thought the vinyl plank is thick, I wanted to make sure I had a solid surface underneath so I wouldn’t accidentally cause it to flex when rolling over it with a chair leg again and again. My first effort was with an expandable foam product (called FastFoam or something similar), which I had recently used to install a new mailbox post for a family friend. What I failed to recognize was that this product is extremely fast acting and pouring an entire bag of it into a pre-dug hole is a much quicker process than trying to carefully fill in an eight foot long shallow track. Once you break the seal on the bag you are supposed to mix it for 15 seconds to start the chemical reaction at which point the foam starts growing rapidly. It begins to harden within 60 seconds and becomes rock hard within 15 minutes. I added to the amount of time it took by starting at the rear of the truck standing outside the back door. Once I had poured the few feet of track I could reach I walked around the side entrance and climbed inside where I continued to poor. It was at that point that I realized two things: foam was starting to exit the bag on it’s own and it was getting hot fast (word of the day: exothermic.) I quickly realized I had screwed up and was mere seconds away from a hot foam fountain. In the few seconds it took me to exit the truck and run-walk towards the garbage can the foam began vigorously spouting out of the opening in the bag and plopping onto the floor. However, I had been able to poor some amount of foam for the entire length of the track before things went sideways. I knew the foam was going to expand and my original concept was that I would be able to simply cut it flush with the floor using a hacksaw blade. This proved nearly impossible and I didn’t get anything close to a flush surface. While the foam does form a surprisingly hard shell, once it’s cut the interior can be deformed easily by pressing on it with your thumb or a tool.
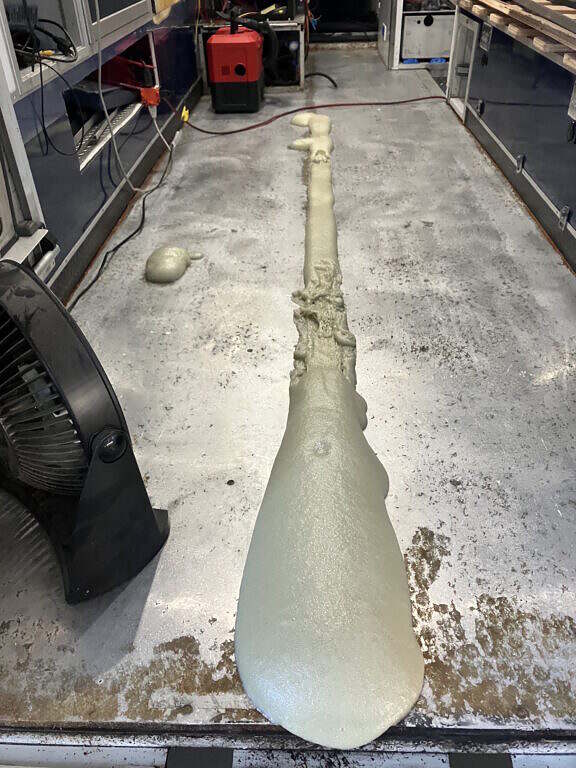
My second solution was to use bondo to fill in the remaining gaps in the foam and level off the surface. Bondo is a two part epoxy with polyester powder that is commonly used for automotive body repair. You can work with it for several minutes after mixing the two parts and it’s much more controllable than the foam. This proved successful and if I had it to do over again I would have filled the entire track with bondo.
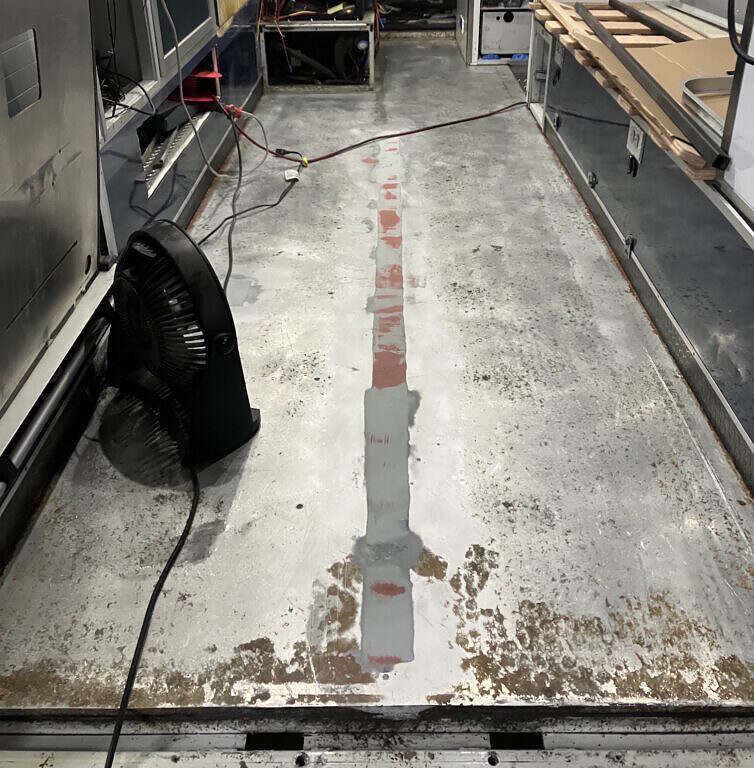
The plank flooring is designed to be installed without adhesive or fasteners, but it also specifically says not to install it in an RV or boat. I was initially concerned that it might have a tendency to shift since it would be in a moving vehicle so my plan was to use strips of double-sided carpet tape applied every couple of feet to hold things secure. However, the floor collectively weighs at least 100 pounds and with the rubber backing and tight fit will be very unlikely to move.
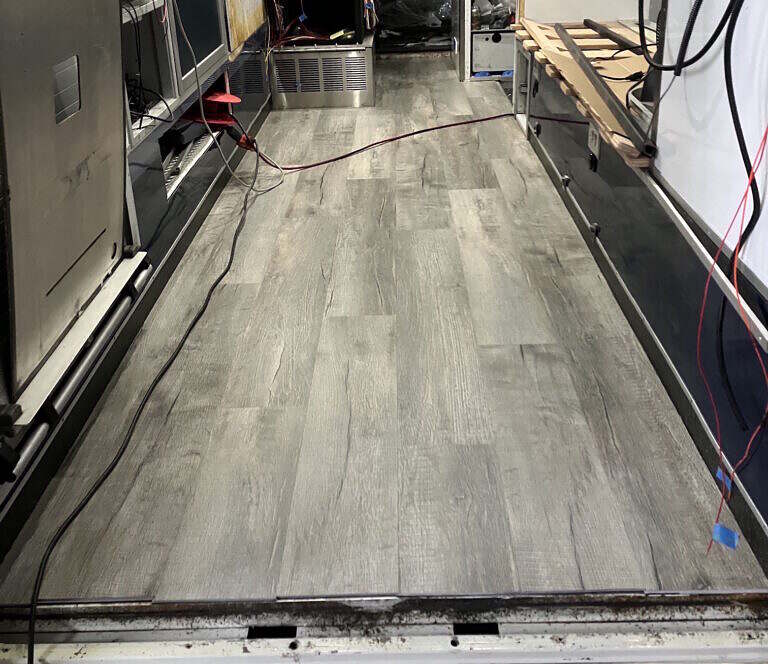