I’ve yet to find anything to suggest corners were cut or something done cheaply in the manufacture of my ambulance. In fact, the exact opposite seems to be true. The module is a masterwork of aluminum fabrication and the thousands of feet of wiring are absolutely first rate. Every single wire is numbered at both ends and an abbreviated description is printed every foot along its entire length, making it comparatively easy to figure out what goes where. It’s also over-engineered as they appear to have used 12 gauge wire in many places, where 14, 16 or even 18 would have been acceptable.
As I dug into the wiring the one thing that threw me at first was the lack of ground wires going to a common bus bar. I could see the ground wires connected to each 12V load, but could not for the life of me find where they were connecting. Upon further dissection I discovered they simply connected the grounds directly to the module body by grinding a spot of raw aluminum near the load and screwing in a terminal to anchor the wire. The module chassis, which is mounted on six enormous bolts isolated by rubber bushings is then grounded to the steel truck chassis by way of large gauge cables.
In the rear, the entire driver’s side module cabinet appears to be made from one huge sheet of 3mm aluminum which was cut, bent and welded to form the various cabinets and CPR seat. I’m assuming this was fabricated outside the unit and installed before the rear was enclosed. Even in the storage beneath the CPR seat, the interior is lined with aluminum diamond plate, which I doubt very few people ever saw or appreciated.
After removing the ceiling I found it was just as over-built as the rest of the module. Besides the small, sectioned areas created by the aluminum square tubing, there are plates of 3mm aluminum welded all along it’s length to provide mounting points for hand-hold bars, IV bags, and vents. (Everything black in the photos of the ceiling and squad bench wall is aluminum. I’m assuming the black coating is some kind of anti-corrosion and noise deadening.)
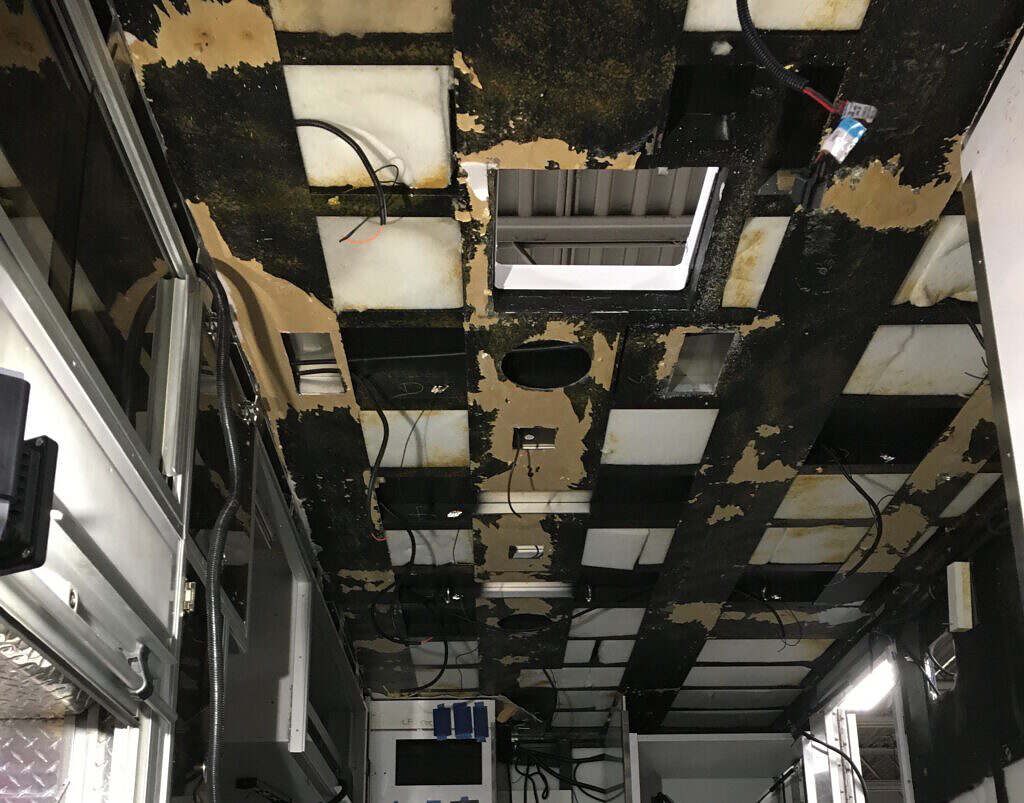
First, the interior walls and ceiling: This are some kind of aluminum/composite sandwich four layers thick. A plastic layer, followed by 2mm aluminum, then a corrugated plastic layer and finally a 1mm layer of aluminum.
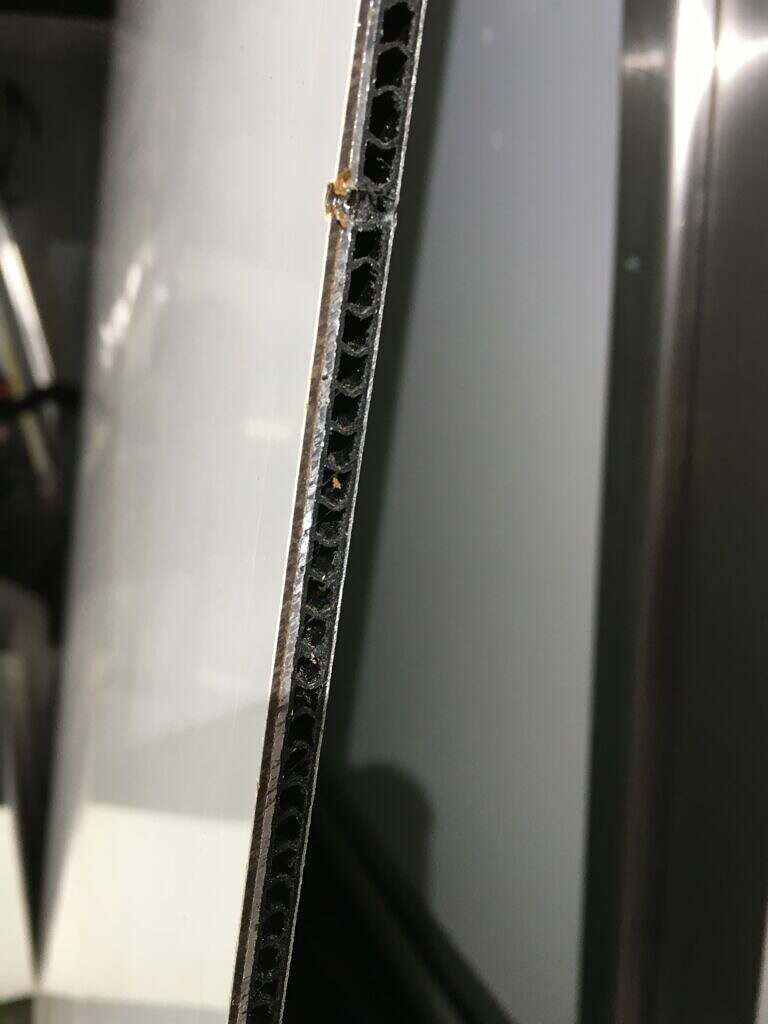
Second, the welded aluminum frame, which is composed of 2″ x 2″ square tube. Many of the top and bottom corners have been reinforced with welded gussets. The photo below is of the wall above the squad bench. I would assume the larger section allowed for an optional window, which I have seen on some other ambulances. Something I could always add later. The compartments formed by the tube frame were filled with a plastic noise insulation. I’ll be replacing that with mineral wool, sealed by reflectix and aluminum tape.
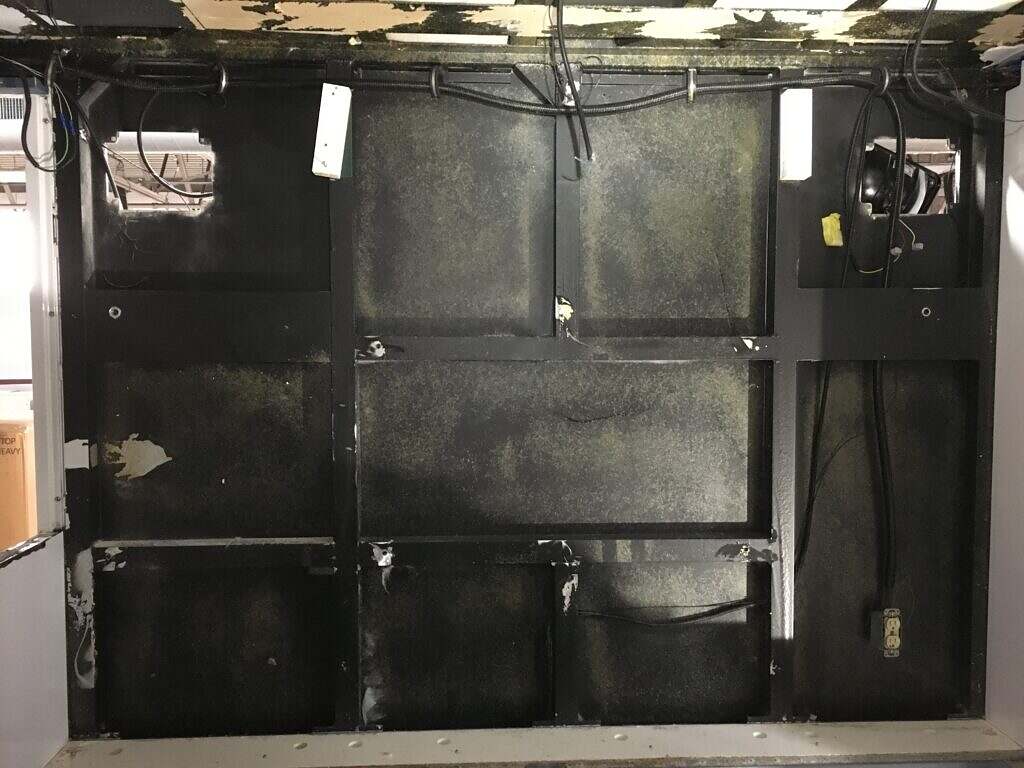
Finally, the outer skin of the module, which is 3mm thick aluminum sheet welded to the subframe.
The external locker doors have some serious heft to them and close with a satisfying ka-thunk. There’s 3mm aluminum on the outside and aluminum diamond plate on the inside enclosing noise deadening pads and insulation. Depending on the size of the door, they are reinforced with horizontal aluminum tube or bar stock. All the module doors swing on heavy duty piano hinges and have two latching hard points, using what I’ve learned are called bear claw latches.
I’ll leave you with this video of a rollover test conducted by Horton EV. This truck is essentially the same as mine, save the the extended cab.